The Basic Principles Of Indonesia Furniture Manufacturers
The Basic Principles Of Indonesia Furniture Manufacturers
Blog Article
Facts About Indonesia Furniture Manufacturers Revealed
Table of ContentsHow Indonesia Furniture Manufacturers can Save You Time, Stress, and Money.Indonesia Furniture Manufacturers - The Facts7 Simple Techniques For Indonesia Furniture ManufacturersThe Facts About Indonesia Furniture Manufacturers RevealedLittle Known Facts About Indonesia Furniture Manufacturers.
There are some drawbacks to acquiring from a furnishings supplier. A furnishings merchant is a firm that offers furniture made by different producers.When you purchase from a furniture store, you're buying a furniture that's currently been made and is prepared to be delivered to your home. Among the benefits of purchasing from a furniture retailer is that you can often see and touch the product prior to you acquire it.
At BH Furnishings, our team believe in establishing new standards for excellence in the manufacturing of industrial furniture - Indonesia furniture manufacturers. Our commitment to innovation has actually led us to accept innovative automation innovation, changing the way we make furnishings and propelling us to the forefront of the market. Gone are the days of manual work dominating the production flooring
State goodbye to production hold-ups and overtime prices. This suggests we not just fulfill but go beyond delivery deadlines, offering our customers with a degree of reliability that standard manufacturing approaches just can't match.
The Main Principles Of Indonesia Furniture Manufacturers
Our manufacturing ability has actually soared, allowing us to fulfill the demands of even the largest tasks without endangering on top quality. As your partner in commercial furnishings options, we can effortlessly scale our output to suit your needs, despite the scale. While typical manufacturing relies greatly on manual work, our automated systems have considerably reduced our dependancy on a large labor force.
Furniture manufacturing is an intricate process that entails different stages, from making and material selection to manufacturing and setting up. At each stage, there is an opportunity of flaws or errors that can jeopardize the quality of the final product. To guarantee that furnishings is of high quality, furnishings suppliers apply quality assurance procedures to determine and remedy any type of issues that might arise during manufacturing.
The examination process ought to cover numerous facets, such as assembly, coating, colour, style, product packaging, labelling, and marking. By applying a rigorous inspection procedure, producers can guarantee their items meet the needed quality, security, and toughness requirements. They likewise give the adaptability to deal with concerns and make corrections before finishing the last item.
The process begins with the raw materials examination to the final setting up of the furniture. The goal is to make sure that the items are without problems, secure, and meet the client's assumptions. Furnishings quality requirements are collections of standards and requirements for furniture manufacturing. They specify the required high quality level of furnishings manufacturing and cover elements such as safety and security, sturdiness, strength, and ecological impact.
The Best Guide To Indonesia Furniture Manufacturers

To guarantee their furnishings products can sustain different weather aspects, including sunlight, rain, snow, and wind, suppliers need to consider worldwide identified requirements that comprise examinations and testing. Right here are several of the requirements to remember: ASTM F1561-03 is a worldwide typical established by the American Area of the International Association for Screening Materials (ASTM).
UL 962 is a worldwide security criterion created by Underwriters Laboratories (UL), an independent international supply safety and security services business. The common uses to house and commercial furnishings, including exterior furnishings.

The Greatest Guide To Indonesia Furniture Manufacturers
It aids to determine problems in the furniture and examine its efficiency and compliance with the called for top quality standards. Right here are the over here steps for carrying out laboratory screening for furnishings: Suppliers collect samples of furnishings elements that need screening. These examples generally represent the different kinds of furniture that they create.
This may involve a mix of various examinations, consisting of toughness screening, longevity screening, safety and security screening, and ecological influence screening. The samples are then tested for numerous quality parameters, such as toughness, longevity, safety and security, and ecological effect. The results are then evaluated to establish whether the items satisfy the required quality standards.

Generally, every retailer furnishings is different. All projects have regarding a month's time in between layout ideation and final manufacturing. This is go to this web-site where the significant challenge lies. Layouts conference consumer benefit Making the most of area use in storage, display, tramp, visitor seats and sidewalks Making sure simplicity of access to items for trials and purchase Creating modular furnishings that is very easy to move and renovate Satisfying security requirements of consumers A fast TAT from layout to production and installation with marginal errors can help deal with the above issues.
See This Report about Indonesia Furniture Manufacturers
A developer can understand the market patterns and be all set with innovative layouts in advance of time. Review here: How DriveWorks Aids You to Reduce Preparation in Production Developers usually need to change the sizes and shapes of furnishings at a moment's notification. These might have different aesthetic and practical demands like front workdesk, and servicing workdesk that differ in measurements.
on an usual system. This combination of sales and ERP functions brings even more visibility on price and prices. It essentially presents CPQ like capability and enables generating quick quotes and amounts for spending plan evaluations and completing orders. Indonesia furniture manufacturers. DriveWorks can auto-generate look what i found production shop drawings with BOMs and DXFs for sheet cutting and boxing
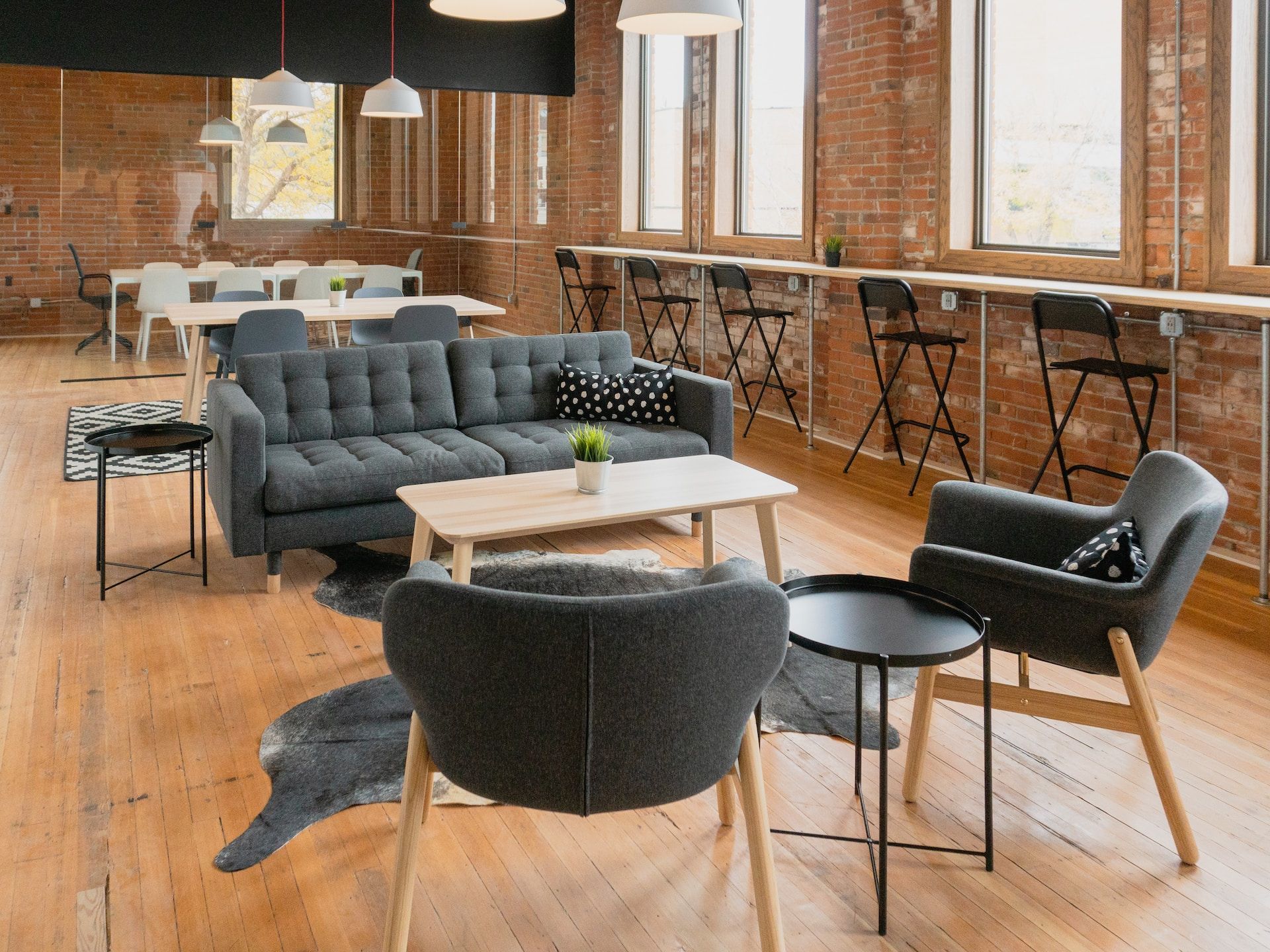
It is a very competitive market, with organizations aiming to maintain up with transforming customer demands and the most recent technical patterns. Today's consumers are extra likely to favor furniture that is personalized and made with lasting products.
Report this page